
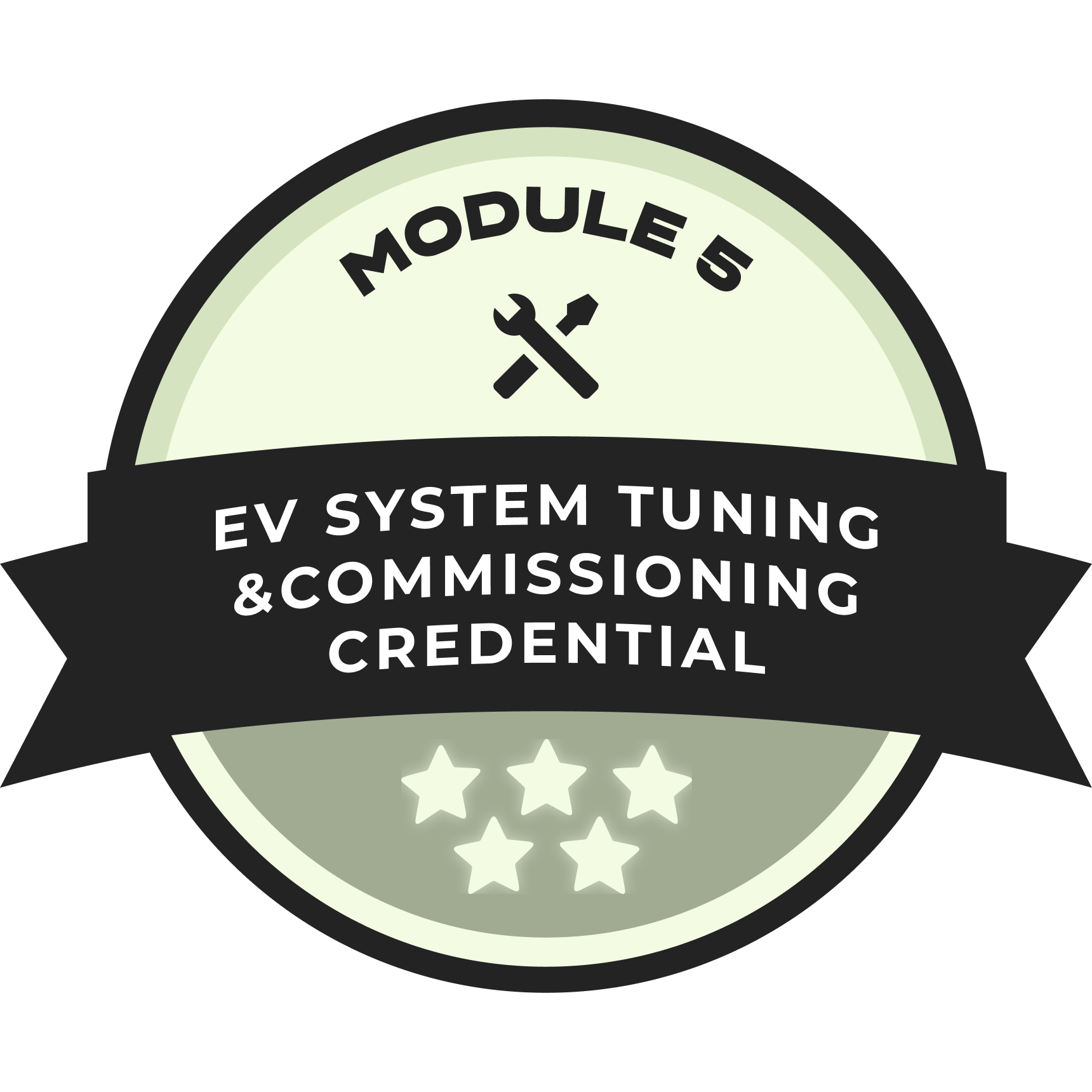
EV Fundamentals Program
Programming, Testing, & Tuning an EV System
By this point in the program you have learned about the best ways to mount and fit an EV system, you have covered how EV systems connect together, and how to do all of this safely. Now it is time to program and tune your system to meet the specific needs of your vehicle.
Due to the nature of an EV being an electronic system, it is likely far more programmable and customizable than the original combustion engine vehicle you started with. For example EVs have programmable torque curves, they can have different modes programmed and accessible in the cab by the flip of a switch, and they can even have programmable modes to allow for single pedal driving.
If you are a seasoned builder with experience with combustion engines, this may be the newest aspect of building an EV for you to learn. Programming your EV will require having access to a properly specced computer, proper software, and the programming manual included with your VCU, BMS, and/or MCU system.
This course is designed as the fifth module of the EV Fundamentals Program
Empty space, drag to resize
EVSC Standards Covered in this Course
2.13 Understand which systems should be monitored during road testing
2.S1.16 Identify best practice testing factors for creating a safe in-shop testing environment
2.S1.17 Demonstrate what testing indicators should be checked when validating the drive system in the shop
2.S1.18 Demonstrate what testing indicators should be checked when validating the charging system in the shop
2.S1.19 Demonstrate what testing indicators should be checked when validating the auxiliary systems in the shop
2.S1.20 Identify the necessary testing factors for creating a safe and effective road-testing environment
2.S4.25 Implement proper placement of jack stands and flow jacks
2.S4.26 Implement proper procedures for safe lift operation
2.S4.27 Identify negative indicators from electric vehicles systems that communicate systems failures and/or sub-optimal vehicle performance
2.S6.29 Understand diagnostic procedures and remedies for on-road system failures or sub-optimal vehicle performance
5.04 Summarize the functions of control pilot and proximity
7.03 Compare and contrast an EV controlled by a VCU and an EV controlled by a controller collection
7.07 Define the CANbus network and identify the general components that use this communication protocol
7.S4.11 Inspect auxiliary systems and lights; repair/replace as needed
7.S5.13 Demonstrate understanding of vehicle controls setup and commissioning processes including how to set limits and cutoffs
7.S5.14 Demonstrate understanding of startup and commissioning processes for an EVCC and how to set charge limits and cut-offs
7.S5.15 Demonstrate understanding of startup and commissioning processes for an BMS and how to set charge limits and cut-offs
7.S5.16 Demonstrate understanding of startup and commissioning processes for auxiliary EV systems such as temperature control units, pumps, and other CAN-based devices
7.S5.17 Demonstrate the proper steps for commissioning, tuning, and testing an EV
7.S7.19 Perform a vehicle multi-point inspection and create vehicle inspection report to document existing vehicle conditions
2.S1.16 Identify best practice testing factors for creating a safe in-shop testing environment
2.S1.17 Demonstrate what testing indicators should be checked when validating the drive system in the shop
2.S1.18 Demonstrate what testing indicators should be checked when validating the charging system in the shop
2.S1.19 Demonstrate what testing indicators should be checked when validating the auxiliary systems in the shop
2.S1.20 Identify the necessary testing factors for creating a safe and effective road-testing environment
2.S4.25 Implement proper placement of jack stands and flow jacks
2.S4.26 Implement proper procedures for safe lift operation
2.S4.27 Identify negative indicators from electric vehicles systems that communicate systems failures and/or sub-optimal vehicle performance
2.S6.29 Understand diagnostic procedures and remedies for on-road system failures or sub-optimal vehicle performance
5.04 Summarize the functions of control pilot and proximity
7.03 Compare and contrast an EV controlled by a VCU and an EV controlled by a controller collection
7.07 Define the CANbus network and identify the general components that use this communication protocol
7.S4.11 Inspect auxiliary systems and lights; repair/replace as needed
7.S5.13 Demonstrate understanding of vehicle controls setup and commissioning processes including how to set limits and cutoffs
7.S5.14 Demonstrate understanding of startup and commissioning processes for an EVCC and how to set charge limits and cut-offs
7.S5.15 Demonstrate understanding of startup and commissioning processes for an BMS and how to set charge limits and cut-offs
7.S5.16 Demonstrate understanding of startup and commissioning processes for auxiliary EV systems such as temperature control units, pumps, and other CAN-based devices
7.S5.17 Demonstrate the proper steps for commissioning, tuning, and testing an EV
7.S7.19 Perform a vehicle multi-point inspection and create vehicle inspection report to document existing vehicle conditions
Empty space, drag to resize
Write your awesome label here.